By Rebekah Morris, CJ Jorgensen and Roland Murphy for AZBEX
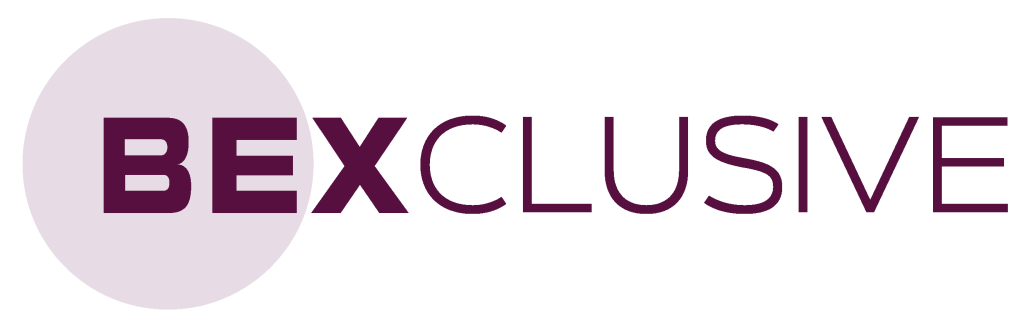
The Phoenix Chapter of the American Society of Professional Estimators recently held its 2025 ASPE Construction Conditions Panel Discussion.
The panel was moderated by BEX Founder and President Rebekah Morris and featured:
- Max Froehlich, Sales Manager, Nucor Steel;
- Bob Karber, Principal, IMCOR;
- Glenn Leier, VP, Wespac Construction;
- Karla Moran, Sr. Manager of the Economic Development Team, SRP;
- Steve Shea, Partner, Hibernian Development, and
- Ben Squires, Project Manager, Butler Design Group.
As she does with most event appearances, Morris began the panel by highlighting various BEX findings around the Arizona construction industry. Arizona’s 2024 construction volume came in at $26.4B. Last year was also marked by a slowing in construction revenue growth. From 2017 to 2023 construction year-over-year revenue growth was steadily growing between 10%-20%. In 2024, revenue growth was at 4.5%.
Construction employment has also been growing since 2017. Employment grew between 5%-10% between 2017 and 2023. Construction employment stalled in 2024, falling by 0.8%.
The Challenge of Pinning Down Tariff Impacts
Morris asked the panel how tariffs have impacted the availability and cost of materials. Tariff-related cost impacts have been difficult to pin down with exact numbers due to the number and variety of factors across different projects.
Karber and Leier explained that dozens of materials are used for each assembly, then dozens of scopes of work make up even the most straightforward project. Taking that a step further, the diverse project types from apartments to roadways to utility projects and beyond will each have a different design and materials need.
The accumulation of hundreds of parts and pieces with changing prices makes it virtually impossible to make an accurate declarative statement on the impacts of tariffs. Everyone knows they are coming, but no one can say with any degree of certainty or precision the impacts.
In a follow-up email, Karber explained there can be weeks or even months between when a contract is signed and when the materials price is finalized. Price fluctuations on materials move much faster than contract negotiations and submittal approval processes.
Leier was asked about other difficult materials to acquire, to which he answered power. Data centers are large power consumers that eat up a lot of supply. He also touched on hoarding materials due to uncertainties. On a positive note, uncertainties have led to earlier submissions and a stronger need for developers and contractors to collaborate.
Shea also found electrical equipment to be problematic and serve as a bottleneck. Much of the construction process is reliant on electrical equipment, which often takes a long time to source. He brought up SRP approvals and wait times as part of the problem. Proposed electrical equipment must go through the approval process twice before SRP looks at it. The process takes a minimum of six months but can last much longer if any hiccups occur.
Moran said that while approval times can take longer than many would hope, they are necessary because without them, bad actors could connect to the system and cause failures. Regarding the shortage of electrical equipment and dubious submittals, Moran reminisced on a client who had submitted a transformer procured from an eBay listing.
Steel and Aluminum Take First Hits
Panelists were asked for specific impacts and notices of price increases due to tariffs.
Moran stated solar panels made overseas are likely to drive up the cost of solar projects needed for power generation.
So far aluminum and steel products have seen real price increases due to tariffs. With that said, however, as a major domestic manufacturer of steel, Froelich gave a thoughtful argument as to why tariffs are needed. He described overseas manufacturing as artificially cheaper due to government subsidies. For example, if India or China provides a 100% subsidy on power supply for major job creators, that cost savings is passed along to buyers, making overseas steel cheaper.
Additionally, bad actors are importing that subsidized steel into either Mexico or Canada, fabricating there, and selling to the U.S. as “Made in Mexico” or “Made in Canada,” thereby circumventing intended tariffs by piggybacking onto existing U.S.-Canada-Mexico trade agreements. Froelich said Nucor is ready and willing to compete with anyone, but it wants a fair and level playing field. Tariffs have the potential to combat inequalities.
No Drive to Onshoring… Yet
The stated goal of tariffs is to bring back manufacturing jobs to the U.S., most notably with new manufacturing plants that will produce well-paying blue-collar jobs and revitalize domestic supply chains.
The panel did not have any examples of manufacturers building new plants due to tariffs. Froelich explained Nucor already had plans and is implementing a robust $20B capital expenditure plan to build new facilities across the nation; however, those plans are not in response to tariff policies.
Morris probed further on this topic: demand has been elevated since at least 2021 for new switchgear and electrical components. Longer lead times on switchgear and components often hold up project openings and are a pinch point in delivering new data center and manufacturing projects.
With long-term demand and a documented gap in projected supply, Morris wanted to know from Moran why more manufacturers have not built factories to increase supply for those items specifically. Moran explained vendors and manufacturers are instead casting a wider net in their supply chain. Karber concurred. Vendors he deals with are not building in the U.S. but rather finding new suppliers worldwide to meet demand.
Froelich chimed in on this topic that building a plant in the US is not only incredibly expensive, but also comes with a large regulatory burden, such as EPA approvals that are not present in other countries.
Lastly, there is no guarantee that the next administration will continue with any tariffs enacted in this current administration. Changes to trade policy could happen quickly, even before a new plant is built or occupied, and certainly before a return on capital investment is realized. If trade policy were to shift back to making imports less expensive than domestically manufactured goods, the investment could potentially be lost. Long-term stability and certainty are needed before firms will be willing to make the massive capital investment and ongoing commitment to employees in a new manufacturing facility.
Current State of Labor
Morris asked the panel to describe their current view of the labor market. Shea answered first by pointing to a recent history of rapidly rising labor rates. He claims this is coming down as workers are now willing to negotiate due to less growth. This is especially true in the multifamily market, which is one of Hibernian’s focuses.
Karber touched on many workers being attracted to Arizona to work on large-scale projects, such as the Taiwan Semiconductor Manufacturing Co. fabrication plants. Currently, many of Arizona’s megaprojects are between phases, which has resulted in a surplus in the workforce. He anticipates the state will return to a labor shortage soon as megaprojects pick back up. (Editor’s Note: TSMC held a groundbreaking this week for the third production fab at its north Phoenix campus.)
Karber is more concerned about the five-year outlook for the labor market. Many people are reaching retirement age, which will cause a swath of professionals with an expansive breadth of knowledge to leave the workforce. He hopes the industry is bringing in enough workers and training them properly.
Morris asked the panelists how many people they currently employ, then followed up with how many they would like to hire. Squires said at Butler Design Group, they have 36 current staff and would add three full-time employees if they wanted to achieve their ideal staff levels.
IMCOR’s Karber stated his current staff level of 200 tradespeople is sufficient for his current backlog, but if he had an unlimited skilled talent pool he could draw from in the next six months, he would take on additional work and grow the company. Moran said SRP has declared it will not be growing headcount, but rather, as demand increases, they will use outside contractors to carry the load.
None of the panel has seen any layoffs due to a lack of work either. Karber pointed out, however, that a lull in workload allows companies to trim underperforming staff, which is likely what is starting to take place. Leier noted that his workforce of 120 staff is the ideal size for his business and still allows him to sleep at night.
Top Industry Concerns
Morris asked the audience to take part in an informal poll. In a show of hands, the audience and panel weighed in on what concerns were the most pressing. The six concerns discussed were:
- Availability of skilled labor;
- Tariffs and materials pricing;
- Costs and availability of funding;
- Uncertainty of federal funding;
- NIMBYs, and
- City approvals.
The largest concerns were shared between tariffs, the approval process and costs/the availability of funding. Some were concerned surrounding the availability of skilled labor. There was concern surrounding NIMBYs, but noticeably less so.
The only panelist to show particular concern for NIMBYs was Moran. When asked for more details, Moran joked, “Power lines are beautiful. It’s okay to have them in your backyard.”
The audience and panel generally were not concerned about federal funding.
Outlook: 2025 May be Low Point
Concluding the event, all the panelists were asked for their outlook on Arizona construction.
Moran reiterated that data centers are going gangbusters in her world. Squires noted that, based on the entitlement work Butler is doing, there are a lot of projects coming.
Shea said good deals are harder to come by due to the high cost of land and capital, but he thinks the senior and assisted living sector is going to explode, especially when interest rates come down.
Froelich, Karber and Leier all had a short-term negative view, saying 2025 was going to be slow, but after that, they all project a large influx of projects.
Leier said Arizona’s diversity in both industry and population has created a resilient and robust market. He ended by saying it is an incredible time to live in Arizona, as its growth is just getting started. He confidently stated there is no place he would rather be.